Advantages Of Rigid Core Click Flooring

In the line of flooring, both for residential or commercial, the product develops year by year. Owing to its special features, SPC rigid core click flooring is the ideal option for ground covering. SPC flooring has what it takes to be the best in the market, first of all, the rigid core makes it much harder and stronger with its intensity as a covering material, combined with the UV layer on top, that makes excellent impact resistance, you will never need to concern one day something falling down to the ground and damage the flooring, or nerve-racking when the chairs moving or sliding on the floor daily which makes some scratches or your naughty baby will create some particular mark when they have fun on the flooring, thus make it looks bad one day. Thanks to the rigid core, it got special protective layer and easy to clean. The second thing is, SPC rigid core flooring compares to the traditional flooring, has more advantage in terms of healthiness, it as a kind of eco-friendly material, is manufactured without involving formaldehyde, making it a perfectly safe choice for installation. Even with newly installed flooring, you can immediately enjoy the space without problem. It saves your time and is available at the moment you need it. So for a instant support, just go to SPC flooring for your solution.
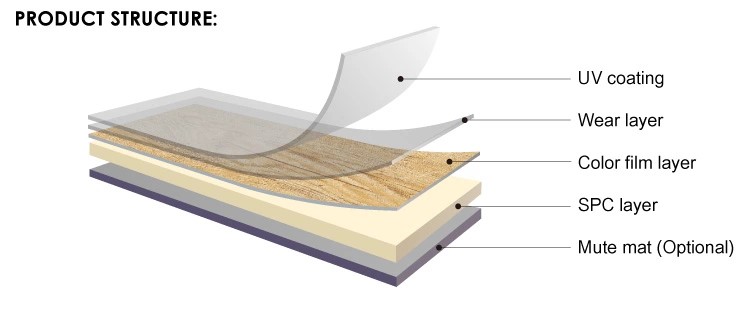
Specification |
|
Surface Texture |
Wood Texture |
Overall Thickness |
3.5mm |
Underlay(Optional) |
IXPE/EVA(1mm/1.5mm) |
Wear Layer |
0.2mm. (8 Mil.) |
Width |
6” (184mm.) |
Length |
36” (1220mm.) |
Finish |
UV Coating |
Click |
![]() |
Application |
Commercial & Residential |
SPC RIGID-CORE PLANK TECHNICAL DATA |
||
Technical Information |
Test Method |
Results |
Dimensional |
EN427 & |
Pass |
Thickness in total |
EN428 & |
Pass |
Thickness of wear layers |
EN429 & |
Pass |
Dimensional Stability |
IOS 23999:2018 & ASTM F2199-18 |
Manufacturing Direction ≤0.02% (82oC @ 6hrs) |
Across Manufacture Direction ≤0.03% (82oC @ 6hrs) |
||
Curling (mm) |
IOS 23999:2018 & ASTM F2199-18 |
Value 0.16mm(82oC @ 6hrs) |
Peel Strength (N/25mm) |
ASTM D903-98(2017) |
Manufacturing Direction 62 (Average) |
Across Manufacture Direction 63 (Average) |
||
Static Load |
ASTM F970-17 |
Residual Indentation:0.01mm |
Residual Indentation |
ASTM F1914-17 |
Pass |
Scratch Resistance |
ISO 1518-1:2011 |
No penetrated the coating at the load of 20N |
Locking Strength(kN/m) |
ISO 24334:2014 |
Manufacturing Direction 4.9 kN/m |
Across Manufacture Direction 3.1 kN/m |
||
Colour Fastness to Light |
ISO 4892-3:2016 Cycle 1 & ISO105–A05:1993/Cor.2:2005& ASTM D2244-16 |
≥ 6 |
Reaction to fire |
BS EN14041:2018 Clause 4.1 & EN 13501-1:2018 |
Bfl-S1 |
ASTM E648-17a |
Class 1 |
|
ASTM E 84-18b |
Class A |
|
VOC Emissions |
BS EN 14041:2018 |
ND – Pass |
ROHS/Heavy Metal |
EN 71-3:2013+A3:2018 |
ND – Pass |
Reach |
No 1907/2006 REACH |
ND – Pass |
Formaldehyde emission |
BS EN14041:2018 |
Class: E 1 |
Phthalate Test |
BS EN 14041:2018 |
ND – Pass |
PCP |
BS EN 14041:2018 |
ND – Pass |
Migration of Certain Elements |
EN 71 – 3:2013 |
ND – Pass |
Packing Information(4.0mm) |
|
Pcs/ctn |
12 |
Weight(KG)/ctn |
22 |
Ctns/pallet |
60 |
Plt/20’FCL |
18 |
Sqm/20’FCL |
3000 |
Weight(KG)/G.W |
24500 |