Durable Commercial Area Floor Material OEM Supplier

Rigid core vinyl flooring was initially designed for commercial settings because of its durability. However, homeowners are gradually accepting this contemporary hard surface because of its countless advantages. It has wide selections of authentic wood and stone looks, and is cost-effective, easy to install and environmental friendly.
Comprised of limestone, SPC flooring has higher density compared to WPC. Its high density offers better resistance from scratches or dents from heavy items that are placed on top of it and makes it less prone to expansion or contraction in cases of extreme temperature change.
In order to reduce the noise when walking, we offer a pre-attached underlay like IXPE to SPC. SPC hard core surface with such underlay is ideal for settings where noise reduction is essential such as classrooms, offices or some spaces in homes.
Rigid core vinyl flooring is also ideal for families with pregnant women or kids, as it’s environmental friendly and formaldehyde free based on tests conducted by the third party organization.
With all these merits, this hard surface is much more affordable than wood or stone flooring. Why not place your order now?!
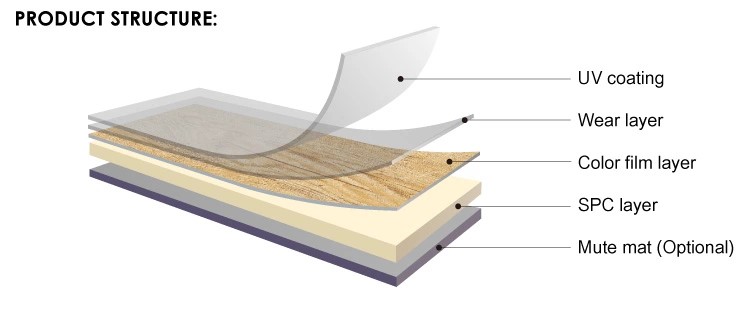
Specification |
|
Surface Texture |
Wood Texture |
Overall Thickness |
4mm |
Underlay(Optional) |
IXPE/EVA(1mm/1.5mm) |
Wear Layer |
0.3mm. (12 Mil.) |
Width |
7.25” (184mm.) |
Length |
48” (1220mm.) |
Finish |
UV Coating |
Click |
![]() |
Application |
Commercial & Residential |
SPC RIGID-CORE PLANK TECHNICAL DATA |
||
Technical Information |
Test Method |
Results |
Dimensional |
EN427 & |
Pass |
Thickness in total |
EN428 & |
Pass |
Thickness of wear layers |
EN429 & |
Pass |
Dimensional Stability |
IOS 23999:2018 & ASTM F2199-18 |
Manufacturing Direction ≤0.02% (82oC @ 6hrs) |
Across Manufacture Direction ≤0.03% (82oC @ 6hrs) |
||
Curling (mm) |
IOS 23999:2018 & ASTM F2199-18 |
Value 0.16mm(82oC @ 6hrs) |
Peel Strength (N/25mm) |
ASTM D903-98(2017) |
Manufacturing Direction 62 (Average) |
Across Manufacture Direction 63 (Average) |
||
Static Load |
ASTM F970-17 |
Residual Indentation:0.01mm |
Residual Indentation |
ASTM F1914-17 |
Pass |
Scratch Resistance |
ISO 1518-1:2011 |
No penetrated the coating at the load of 20N |
Locking Strength(kN/m) |
ISO 24334:2014 |
Manufacturing Direction 4.9 kN/m |
Across Manufacture Direction 3.1 kN/m |
||
Colour Fastness to Light |
ISO 4892-3:2016 Cycle 1 & ISO105–A05:1993/Cor.2:2005& ASTM D2244-16 |
≥ 6 |
Reaction to fire |
BS EN14041:2018 Clause 4.1 & EN 13501-1:2018 |
Bfl-S1 |
ASTM E648-17a |
Class 1 |
|
ASTM E 84-18b |
Class A |
|
VOC Emissions |
BS EN 14041:2018 |
ND – Pass |
ROHS/Heavy Metal |
EN 71-3:2013+A3:2018 |
ND – Pass |
Reach |
No 1907/2006 REACH |
ND – Pass |
Formaldehyde emission |
BS EN14041:2018 |
Class: E 1 |
Phthalate Test |
BS EN 14041:2018 |
ND – Pass |
PCP |
BS EN 14041:2018 |
ND – Pass |
Migration of Certain Elements |
EN 71 – 3:2013 |
ND – Pass |
Packing Information(4.0mm) |
|
Pcs/ctn |
12 |
Weight(KG)/ctn |
22 |
Ctns/pallet |
60 |
Plt/20’FCL |
18 |
Sqm/20’FCL |
3000 |
Weight(KG)/G.W |
24500 |